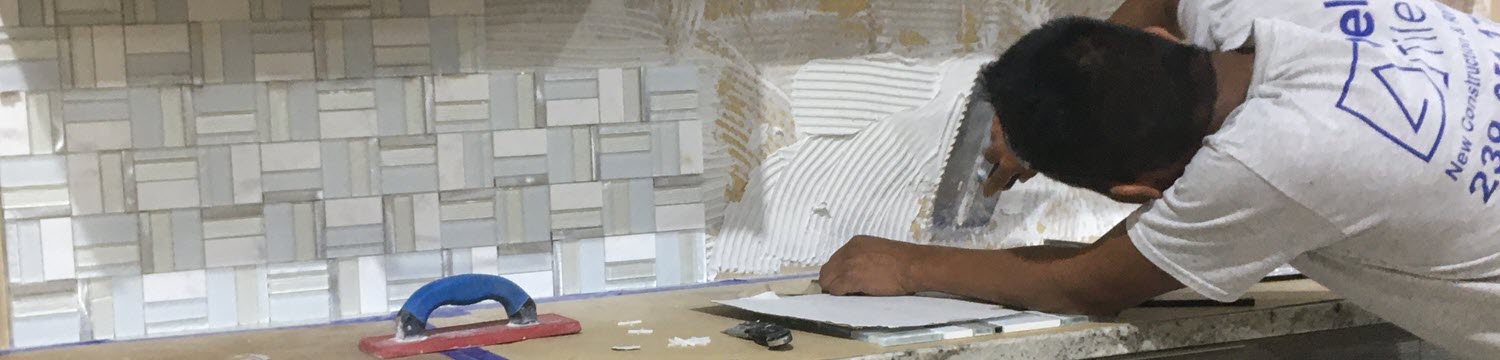
Interested in Learning About Tile And More?
Do you have questions about tile, stone, mosaics, decorative tile, or any of the other products you can find at Tile Outlets of America?
You've come to the right place.
Our associates have years of experience in the tile and stone business and we have plenty to share with you!
Here's what you can expect in this section about learning:
- FAQs
- How to Care for Tile, Stone, and more
- What to Consider When Selecting Tile, Stone, and Mosaics
- What You'll Need to Install Tile
- Product Knowledge Videos
If you can't find what you're looking for, simply Contact Us to let us know!
Our associates have years of experience in the tile and stone business and we have plenty to share with you!
Here's what you can expect in this section about learning:
- FAQs
- How to Care for Tile, Stone, and more
- What to Consider When Selecting Tile, Stone, and Mosaics
- What You'll Need to Install Tile
- Product Knowledge Videos
If you can't find what you're looking for, simply Contact Us to let us know!